Stel je een fabricageproces voor dat de ingewikkelde details en ontwerpvrijheid van kunststof spuitgieten combineert met de ongeëvenaarde sterkte en duurzaamheid van metaal. Dat is de magie van Metaal spuitgieten (MIM), een doorbraak in de wereld van metaalbewerking.
Wat is metaalspuitgieten (MIM)?
MIM is een bijna-netvormige productietechniek die gebruik maakt van een uniek mengsel van metaalpoeder en een polymeer bindmiddel. Deze combinatie, bekend als grondstof, gedraagt zich als een kneedbare pasta. Bij het MIM-proces wordt deze grondstof onder hoge druk strategisch in een vormholte geïnjecteerd, waardoor de gewenste complexe geometrie wordt nagebootst. Hier volgt een opsplitsing van het MIM proces in de belangrijkste stappen:
- Grondstofvoorbereiding: Fijn gepoederd metaal, meestal roestvrij staal, staallegeringen of zelfs exotische materialen zoals wolfraamcarbide, wordt zorgvuldig gemengd met een bindmiddelsysteem. Dit bindmiddel zorgt voor de vloeibaarheid van het mengsel tijdens het spuitgieten.
- Vormgeven: De voorbereide grondstof wordt onder hoge druk in een precies ontworpen vormholte gespoten. Dit bootst de ingewikkelde bijna-netvorm van het gewenste metalen onderdeel na.
- Ontbinden: Na het gieten moet het bindmiddel uit het gegoten onderdeel worden verwijderd. Dit delicate proces, vaak debinding genoemd, kan thermische technieken (verwarming) of solvent debinding omvatten, afhankelijk van het gekozen bindmiddelsysteem.
- Sinteren: Het afgebroken onderdeel, nu een fragiele structuur van metaalpoeder, ondergaat een sinterproces bij hoge temperatuur in een gecontroleerde atmosfeer. In deze cruciale stap smelten de metaaldeeltjes samen, waardoor de gewenste sterkte en dichtheid voor het uiteindelijke onderdeel wordt bereikt.
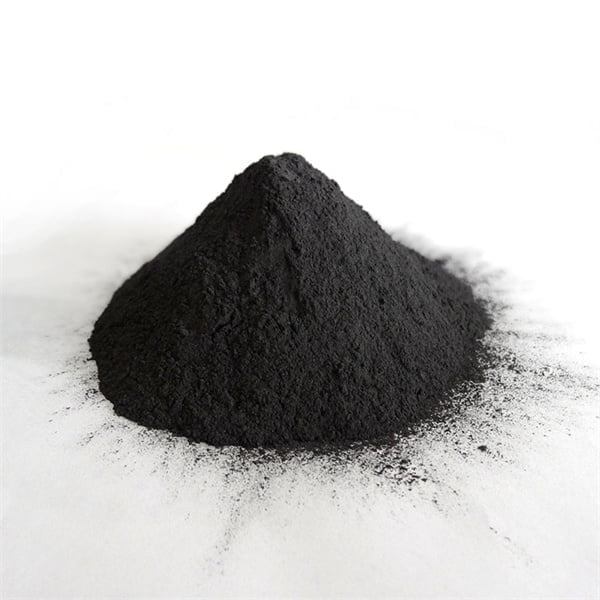
De voordelen van Metaal spuitgieten (MIM)
MIM biedt een aantal overtuigende voordelen die het een veelgevraagd proces maken voor verschillende industrieën:
- Complexe geometrieën: In tegenstelling tot traditionele bewerkingstechnieken die moeite hebben met ingewikkelde vormen, blinkt MIM uit in de productie van onderdelen met complexe kenmerken, nauwe toleranties en dunne wanden. Dit opent deuren voor innovatieve ontwerpen die voorheen moeilijk of onmogelijk te realiseren waren met conventionele methoden.
- Hoge precisie en herhaalbaarheid: MIM maakt gebruik van de precisie van spuitgieten, wat resulteert in zeer consistente onderdelen met minimale variaties in afmetingen. Dit leidt tot betrouwbare prestaties en minder nabewerkingen.
- Massaproductie: MIM is een geschikt proces voor grote productieseries. Zodra de matrijs is ingesteld, kan MIM efficiënt een groot aantal identieke onderdelen maken, waardoor het ideaal is voor toepassingen waarbij een constante kwaliteit en grote hoeveelheden vereist zijn.
- Veelzijdigheid van materiaal: MIM heeft een breed scala aan compatibele materialen, van gewone roestvaste staalsoorten en gereedschapsstaal tot exotische opties zoals titanium en inconel. Hierdoor kan het optimale materiaal worden gekozen op basis van de specifieke sterkte, corrosiebestendigheid of andere prestatievereisten van de toepassing.
- Kosteneffectiviteit: Vergeleken met traditionele bewerkingstechnieken kan MIM, vooral voor complexe geometrieën, aanzienlijke kostenbesparingen opleveren. De bijna-net-vorm mogelijkheid minimaliseert materiaalverspilling en vermindert de noodzaak voor uitgebreide machinale bewerkingen.
Toepassingen van metaalspuitgieten (MIM)
De diverse voordelen van MIM hebben het tot een populaire keuze gemaakt in een breed spectrum van industrieën. Hier volgen enkele prominente voorbeelden:
- Automobiel: MIM schittert in de auto-industrie, waar ingewikkelde onderdelen worden gemaakt zoals tandwielen, tandwielen, kleponderdelen en onderdelen van het brandstofsysteem die bekend staan om hun duurzaamheid en maatnauwkeurigheid.
- Medische hulpmiddelen: De biocompatibele aard van bepaalde MIM-materialen maakt het perfect voor medische toepassingen. MIM wordt gebruikt om ingewikkelde chirurgische instrumenten, implantaten en onderdelen voor verschillende medische apparaten te maken.
- Consumentenelektronica: De mogelijkheid om kleine, complexe onderdelen met hoge precisie te produceren, maakt MIM ideaal voor de consumentenelektronica-industrie. MIM vindt toepassingen in connectoren, behuizingen en interne onderdelen voor verschillende elektronische apparaten.
- Ruimtevaart en defensie: De hoge eisen van de lucht- en ruimtevaart en defensie zijn zeer geschikt voor MIM. MIM produceert lichtgewicht componenten met hoge sterkte voor vliegtuigen, ruimtevaartuigen en wapensystemen.
Verder dan de voordelen: Overwegingen voor MIM
Hoewel MIM een overvloed aan voordelen biedt, is het essentieel om een aantal factoren in overweging te nemen voordat je het voor jouw specifieke toepassing kiest:
- Beperkingen in onderdeelgrootte: MIM heeft momenteel beperkingen op de maximale grootte van onderdelen die het kan produceren. Onderdelen die een bepaald volume overschrijden zijn wellicht beter geschikt voor traditionele metaalbewerkingstechnieken.
- Materiële beperkingen: Hoewel MIM een breed scala aan materialen biedt, zijn sommige exotische of speciale legeringen mogelijk niet gemakkelijk verkrijgbaar of kosteneffectief via MIM.
- Ontwikkelingskosten: Het opzetten van het MIM-proces voor een nieuw onderdeel vereist een investering vooraf in de ontwikkeling van matrijzen en procesoptimalisatie. Deze kostenfactor moet worden afgewogen tegen het potentiële productievolume en de voordelen op lange termijn.
MIM begrijpen: een technisch dieptepunt
Voor degenen die geïnteresseerd zijn in de technische details van MIM, volgen hier enkele belangrijke aspecten:
Grondstofselectie: De keuze van de juiste grondstof is cruciaal voor succesvol MIM. Hier zijn enkele belangrijke aspecten om rekening mee te houden:
-
Metaalpoeder:
- Deeltjesgrootte en -verdeling: De grootte en verdeling van het metaalpoeder hebben een grote invloed op de uiteindelijke eigenschappen van het onderdeel. Fijnere poeders maken over het algemeen nauwere toleranties en gladdere afwerkingen mogelijk, maar ze kunnen ook lastiger te verwerken zijn vanwege problemen met de vloeibaarheid. Een uitgebalanceerde deeltjesgrootteverdeling heeft vaak de voorkeur.
- Poeder morfologie: De vorm van de metaaldeeltjes speelt ook een rol. Bolvormige poeders hebben de neiging om beter te vloeien en dichter opeen te zitten, wat leidt tot een betere sterkte en maatnauwkeurigheid.
- Bindmiddelensysteem: Het bindmiddelsysteem werkt als een tijdelijke lijm die het metaalpoeder bij elkaar houdt tijdens het vormen en afbinden. Verschillende bindmiddelsystemen hebben verschillende eigenschappen, zoals thermische stabiliteit, afbindgedrag en compatibiliteit met het gekozen afbindproces.
Ontwerp van mallen voor MIM:
MIM-mallen hebben overeenkomsten met plastic spuitgietmallen, maar vereisen specifieke overwegingen voor het gedrag van metaalpoeder:
- Poortontwerp: Het ontwerp van de poorten, die de ingang vormen voor de grondstof in de matrijsholte, moet een goede doorstroming garanderen en turbulentie, die tot defecten kan leiden, tot een minimum beperken.
- Ontluchting: Ontluchtingskanalen zijn cruciaal om ingesloten lucht te laten ontsnappen tijdens het inspuiten, om holtes te voorkomen en om ervoor te zorgen dat het product volledig wordt gevuld.
- Opzethoeken: Trekhoeken op de matrijswanden zijn essentieel om het gevormde onderdeel na afkoeling gemakkelijk te kunnen verwijderen.
Ontbindingstechnieken in MIM:
Zoals eerder vermeld, is ontbinden de kritische stap om het bindmiddel van het spuitgietproduct te verwijderen. Hier volgt een uitsplitsing van de twee primaire ontbindingstechnieken:
- Thermisch ontbinden: Bij deze methode wordt het spuitgietproduct geleidelijk verwarmd in een gecontroleerde atmosfeer. Naarmate de temperatuur stijgt, wordt het bindmiddel afgebroken en ontbonden, waardoor de metaalpoederstructuur achterblijft. Het verwarmingsprofiel moet zorgvuldig worden ontworpen om ervoor te zorgen dat het bindmiddel volledig wordt verwijderd zonder de delicate metaalstructuur te beschadigen.
- Ontbinding met oplosmiddelen: Deze techniek maakt gebruik van een oplosmiddel dat het bindmiddelsysteem selectief oplost. Het spuitgietproduct wordt ondergedompeld in het oplosmiddel, waardoor het bindmiddel uitloogt terwijl het metaalpoeder intact blijft. Ontbinding met oplosmiddelen kan sneller zijn dan thermisch ontbinden, maar vereist mogelijk speciale behandeling en verwijdering van het gebruikte oplosmiddel.
Sinteren in MIM:
Sinteren is de laatste fase van het MIM-proces, waarin het gedebuteerde metaalpoeder verandert in een vast, functioneel onderdeel. Tijdens het sinteren wordt het onderdeel blootgesteld aan hoge temperaturen (meestal tussen 1/2 en 2/3 van het smeltpunt van het metaal) in een gecontroleerde atmosfeer. Deze hoge temperatuur bevordert de diffusiebinding tussen de metaaldeeltjes, wat leidt tot verdichting en een aanzienlijke verbetering van de sterkte en andere mechanische eigenschappen.
Kwaliteitscontrole in MIM:
Het handhaven van een consistente kwaliteit is van het grootste belang bij MIM-productie. Hier volgen enkele essentiële maatregelen voor kwaliteitscontrole:
- Karakterisering van grondstoffen: Het regelmatig testen van de eigenschappen van de grondstof, zoals de verdeling van de metaalpoedergrootte en het bindmiddelgehalte, zorgt voor consistent materiaalgedrag tijdens de verwerking.
- Dimensionale inspectie: De afmetingen van de spuitgietproducten worden nauwkeurig gecontroleerd om er zeker van te zijn dat ze voldoen aan de ontwerpspecificaties en nauwe toleranties behouden.
- Dichtheidsmeting: De dichtheid van de gesinterde onderdelen is een kritische indicator voor hun sterkte en prestaties. Er kunnen verschillende technieken, zoals het principe van Archimedes of pyknometrie, worden gebruikt om de dichtheid te meten.
- Microstructuuranalyse: Microscopisch onderzoek van de microstructuur van het gesinterde onderdeel onthult informatie over korrelgrootte, porositeit en mogelijke defecten.
De toekomst van Metaal spuitgieten
MIM is een technologie die voortdurend in ontwikkeling is, met voortdurende onderzoeks- en ontwikkelingsinspanningen gericht op:
- Uitbreiding van het materiaalbereik: Het onderzoek naar nieuwe materialen en bindmiddelsystemen die compatibel zijn met MIM, verbreedt de toepassingsmogelijkheden van dit veelzijdige proces.
- Verbeterde procesefficiëntie: Het onderzoek is gericht op het optimaliseren van de debinding- en sinterfase om de cyclustijden te verkorten en de algehele productie-efficiëntie te verbeteren.
- Complexiteit van geavanceerde onderdelen: Ontwikkelingen in matrijsontwerp en materiaalwetenschap verleggen de grenzen van de haalbare onderdeelcomplexiteit door MIM.
Metaal spuitgieten biedt een unieke combinatie van ontwerpvrijheid, materiaalveelzijdigheid en kosteneffectiviteit voor een groot aantal industrieën. Naarmate de technologie zich verder ontwikkelt, kunnen we nog meer innovatieve toepassingen en vooruitgang verwachten in de opwindende wereld van MIM.
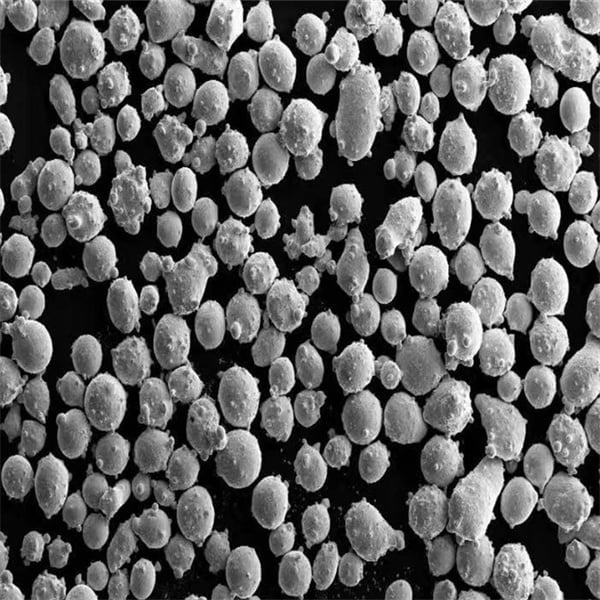
FAQ
Tabel 1: Veelgestelde vragen over metaalspuitgieten (MIM)
Vraag | Antwoord |
---|---|
Wat zijn de typische beperkingen voor de afmetingen van MIM-onderdelen? | De maximale grootte van MIM-onderdelen is over het algemeen beperkt tot een paar kubieke centimeter. Deze beperking is te wijten aan problemen met de grondstofstroom en het zorgen voor uniforme ontbinding in grotere onderdelen. |
Kan MIM worden gebruikt voor prototypes? | Ja, MIM kan een haalbare optie zijn voor het maken van prototypes van complexe metalen onderdelen, vooral als een hoge mate van nauwkeurigheid en trouw aan het uiteindelijke ontwerp vereist is. Er moet echter rekening worden gehouden met de aanloopkosten van matrijsontwikkeling. |
Wat zijn de voordelen van MIM in vergelijking met traditionele machinale bewerking? | MIM biedt diverse voordelen ten opzichte van traditionele machinale bewerking, waaronder: In staat om complexe geometrieën met nauwe toleranties te produceren Grotere ontwerpvrijheid voor ingewikkelde functies Hoge precisie en herhaalbaarheid voor consistente onderdelen Efficiënte massaproductie voor grote hoeveelheden Minder materiaalverspilling vergeleken met subtractieve technieken |
Wat zijn de nadelen van MIM in vergelijking met traditionele machinale bewerking? | Er zijn ook enkele beperkingen waar je rekening mee moet houden bij MIM: Beperkingen in onderdeelgrootte vergeleken met technieken zoals gieten of smeden Materiaalbeperkingen voor bepaalde exotische of speciale legeringen Hogere aanloopkosten door ontwikkeling schimmel De afwerking van het oppervlak komt mogelijk niet overeen met uitzonderlijk gladde afwerkingen die kunnen worden bereikt door polijsten of slijpen |
Wat zijn enkele factoren die je moet overwegen bij de keuze tussen MIM en traditionele metaalbewerking? | De ideale keuze hangt af van je specifieke toepassing. Hier zijn enkele belangrijke factoren om af te wegen: Complexiteit onderdeelgeometrie Vereisten voor productievolume Behoeften voor materiaalselectie Kostenoverwegingen, inclusief initiële investering en potentiële besparingen Eisen aan oppervlakteafwerking |
Wat zijn enkele toekomstige trends in MIM-technologie? | De onderzoeks- en ontwikkelingsinspanningen voor MIM zijn gericht op het uitbreiden van het materiaalgamma, het verbeteren van de procesefficiëntie voor snellere cyclustijden en het verleggen van de grenzen van de haalbare onderdeelcomplexiteit. |
Wat zijn enkele typische toepassingen van MIM? | MIM vindt toepassingen in een breed scala aan industrieën, waaronder: Automobiel (tandwielen, tandwielen, kleponderdelen) Medische hulpmiddelen (chirurgische instrumenten, implantaten) Consumentenelektronica (connectoren, behuizingen) Luchtvaart en defensie (lichtgewicht componenten met hoge sterkte) |
Wat zijn de verschillende soorten grondstoffen die bij MIM worden gebruikt? | De grondstof voor MIM bestaat meestal uit een metaalpoeder (bijvoorbeeld roestvrij staal, staallegeringen, titanium) gemengd met een polymeer bindmiddelsysteem. Het specifieke type metaalpoeder en bindmiddel hangt af van de gewenste uiteindelijke eigenschappen van het onderdeel. |
Wat zijn de verschillende ontbindingstechnieken die bij MIM worden gebruikt? | Er zijn twee primaire ontbindingstechnieken: Thermisch ontbinden: Geleidelijke verhitting om het bindmiddel te verwijderen. Ontbinding met oplosmiddel: Een oplosmiddel gebruiken om het bindmiddel selectief op te lossen. |
Het juiste proces kiezen: MIM vs. traditionele metaalbewerking
De keuze tussen MIM en traditionele metaalbewerkingstechnieken hangt af van verschillende factoren die specifiek zijn voor uw toepassing. Hier zijn enkele belangrijke overwegingen om uw keuze te begeleiden:
- Deelgeometrie: Als uw onderdeel complexe vormen, nauwe toleranties en ingewikkelde details heeft, biedt MIM een aanzienlijk voordeel.
- Productievolume: De efficiëntie en herhaalbaarheid van MIM maken het een aantrekkelijke optie voor productieruns met hoge volumes.
- Materiaalkeuze: Zorg ervoor dat het materiaal dat je nodig hebt compatibel is met MIM. Als je een exotische legering nodig hebt die niet gemakkelijk verkrijgbaar is in MIM, dan is traditionele metaalbewerking misschien de beste oplossing.
- Kostenoverwegingen: Houd rekening met de aanloopkosten van matrijsontwikkeling voor MIM versus de potentiële materiaalverspilling en langere productietijden van traditionele technieken voor complexe onderdelen.
- Vereisten voor oppervlakteafwerking: Als een onberispelijke afwerking van het oppervlak van het grootste belang is, kunnen traditionele technieken zoals polijsten nodig zijn.
Conclusie
Metaal Injection Molding (MIM) is een krachtig en veelzijdig productieproces dat een unieke combinatie biedt van ontwerpvrijheid, materiaalopties en kosteneffectiviteit voor een groot aantal toepassingen. Door de voordelen en beperkingen te begrijpen en hoe het zich verhoudt tot traditionele metaalbewerkingstechnieken, kunt u weloverwogen beslissingen nemen om MIM in te zetten voor uw specifieke behoeften en het potentieel voor innovatieve en hoogwaardige metalen onderdelen ontsluiten.