Heb je er ooit van gedroomd om complexe metalen voorwerpen uit het niets te toveren? Nou, met Direct Metal Laser Sintering (DMLS) technologie wordt die droom werkelijkheid. DMLS, ook bekend als Selective Laser Melting (SLM), is een revolutionair 3D printproces dat gebruik maakt van een krachtige laser om metaalpoederdeeltjes laag voor laag nauwkeurig samen te smelten om ingewikkelde en functionele metalen onderdelen te maken.
Stel je voor dat je een ingewikkeld tandwiel of een lichtgewicht luchtvaartcomponent met interne kanalen bouwt, allemaal vanuit een digitaal bestand - dat is de kracht van DMLS. Maar hoe gebeurt deze magie precies? Zet je schrap, want we gaan je stap voor stap inwijden in de fascinerende wereld van DMLS.
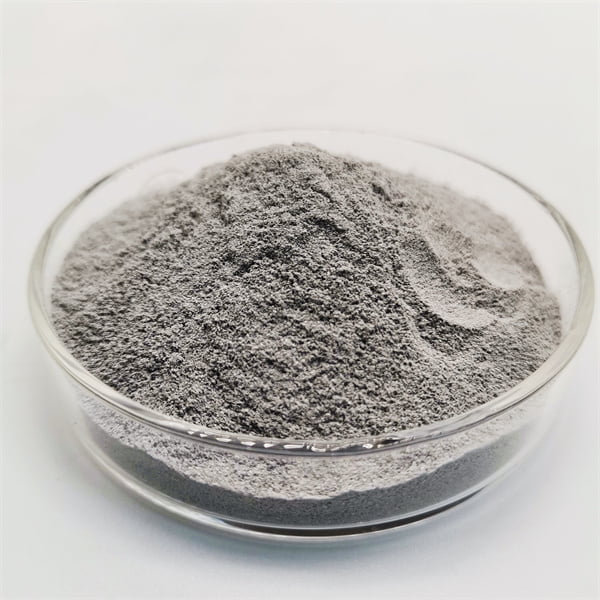
De bouwstenen: Een blik op DMLS Metaalpoeders
De basis van elke DMLS-creatie ligt in het metaalpoeder zelf. Deze fijne, metalen korrels, meestal variërend van 15 tot 63 micron groot (dat is ongelooflijk klein!), zijn verkrijgbaar in verschillende smaken, elk met unieke eigenschappen voor specifieke toepassingen. Hier is een voorproefje van enkele van de populairste DMLS metaalpoederopties:
Metaalpoeder | Samenstelling | Eigenschappen | Toepassingen |
---|---|---|---|
Roestvrij staal 316L | 16-18% chroom, 10-14% nikkel, 2% molybdeen | Uitstekende corrosiebestendigheid, hoge sterkte, biocompatibel | Medische implantaten, onderdelen voor de ruimtevaart, juwelen |
Titaan 6Al-4V (graad 23) | 90% Titanium, 6% Aluminium, 4% Vanadium | Hoge sterkte-gewichtsverhouding, goede biocompatibiliteit, uitstekende corrosiebestendigheid | Ruimtevaartonderdelen, medische implantaten, sportartikelen |
Inconel 625 | Superlegering op basis van nikkel-chroom | Uitzonderlijke sterkte bij hoge temperaturen, corrosiebestendigheid | Turbinebladen, warmtewisselaars, kernreactoren |
Aluminium AlSi10Mg | Aluminiumlegering met 10% silicium en 0,5% magnesium | Lichtgewicht, goede corrosiebestendigheid, hoge thermische geleidbaarheid | Auto-onderdelen, koellichamen, elektronicabehuizingen |
Koper | 100% Koper | Hoge elektrische geleidbaarheid, goede thermische geleidbaarheid | Warmtewisselaars, elektrische componenten, golfgeleiders |
Gereedschapsstaal (H13) | Gelegeerd staal met hoog chroomgehalte | Hoge slijtvastheid, goede thermische stabiliteit | Mallen, matrijzen, snijgereedschappen |
Nikkel | 100% Nikkel | Uitstekende corrosiebestendigheid, goede vervormbaarheid | Apparatuur voor chemische verwerking, elektrische onderdelen, warmtewisselaars |
Kobaltchroom (CoCrMo) | Kobalt-chroomlegering met molybdeen | Hoge sterkte, slijtvast, biocompatibel | Medische implantaten, tandprothesen, slijtdelen |
Goud | 100% Goud | Hoge ductiliteit, smeedbaarheid, uitstekende corrosiebestendigheid | Sieraden, elektronica, decoratieve toepassingen |
Deze tabel geeft een kijkje in de diverse wereld van DMLS metaalpoeders. Elk materiaal heeft unieke sterke punten, waardoor het geschikt is voor een breed scala aan toepassingen. Bij de keuze van een metaalpoeder spelen factoren zoals de gewenste mechanische eigenschappen, corrosiebestendigheid, gewicht en biocompatibiliteit (voor medische toepassingen) allemaal een cruciale rol.
Verder dan de tabel: Een diepere duik in metaalpoedereigenschappen
Het is belangrijk om te begrijpen dat deze metaalpoeders niet zomaar stof zijn. Ze zijn zorgvuldig samengesteld voor optimale prestaties tijdens het DMLS-proces. Hier zijn enkele belangrijke kenmerken om rekening mee te houden:
- Deeltjesgrootte en -verdeling: Een consistente deeltjesgrootte en -distributie zijn cruciaal voor een soepele poederstroom en gelijkmatig lasersmelten.
- Sfericiteit: Bolvormige deeltjes bieden een betere vloeibaarheid en verpakkingsdichtheid, wat leidt tot een uniformer bouwproces.
- Vloeibaarheid: Het vermogen van het poeder om vrij te stromen in de DMLS-machine is essentieel voor een consistente laagvorming.
- Schijnbare dichtheid: Dit verwijst naar de verhouding tussen de massa van het poeder en het totale volume. Bij een hogere schijnbare dichtheid kan er meer materiaal in elke laag worden verpakt, wat resulteert in een dichter eindproduct.
- Laserabsorptie: Het vermogen van het metaalpoeder om de energie van de laser efficiënt te absorberen dicteert het smeltproces en de algehele bouwkwaliteit.
Fabrikanten gaan heel ver om ervoor te zorgen dat hun DMLS metaalpoeders aan deze strenge eisen voldoen. Door deze eigenschappen zorgvuldig te controleren, creëren ze poeders die speciaal ontworpen zijn voor optimale DMLS-prestaties.
Van digitale dromen naar metalen werkelijkheid: Het DMLS proces stap voor stap
Nu we de bouwstenen hebben bekeken, kunnen we ons gaan verdiepen in de fascinerende wereld van DMLS zelf. Hier volgt een uitsplitsing van het proces, stap voor stap:
1. Kies het juiste metaalpoeder: Zoals eerder besproken, is het selecteren van het juiste metaalpoeder cruciaal voor het bereiken van de gewenste eigenschappen in het uiteindelijke onderdeel.
2. Maak een 3D-model met behulp van 3D-modelleringssoftware: De magie van DMLS begint met een digitale representatie van het gewenste object. Met 3D-modelleringssoftware, vergelijkbaar met de beitel van een beeldhouwer in het digitale tijdperk, kunnen ingenieurs ingewikkelde geometrieën ontwerpen die onmogelijk te maken zijn met traditionele productiemethoden. Deze 3D-modellen bepalen elk detail van het uiteindelijke onderdeel, van de algemene vorm tot interne kanalen en ingewikkelde kenmerken.
3. Bereid het bouwplatform voor: Stel je een digitaal canvas voor dat tot leven komt. Het platform van de DMLS machine vormt de basis waarop het metalen object laag voor laag wordt opgebouwd. Dit platform wordt zorgvuldig gereinigd en genivelleerd om een glad en consistent startpunt voor het bouwproces te garanderen.
4. Leg het metaalpoeder op het afdrukplatform: Een dunne laag metaalpoeder, meestal 20 tot 100 micron dik, wordt gelijkmatig op het bouwplatform aangebracht. Deze laag fungeert als de eerste bouwsteen voor het object. Verschillende technieken, zoals een mescoatsysteem of een rolmechanisme, kunnen worden gebruikt om een uniforme en consistente poederlaag te verkrijgen.
5. De laser smelt de magie: Hier gebeurt de echte magie. Een krachtige laserstraal, nauwkeurig geleid door het digitale 3D-model, scant over het metaalpoederbed en smelt de deeltjes selectief samen. De vermogensdichtheid en het scantraject van de laser worden nauwkeurig geregeld om de gewenste geometrie voor elke laag te creëren. Terwijl de laser het poeder smelt, versmelt het de deeltjes tot een vaste massa, waardoor het object effectief laag voor laag wordt opgebouwd.
6. Laag voor laag krijgt het object vorm: Het DMLS-proces volgt een zich herhalende cyclus. Zodra de eerste laag gesmolten is, wordt er een nieuwe laag metaalpoeder op aangebracht. De laser scant vervolgens over deze nieuwe laag, smelt het poeder en versmelt het met de eerder opgebouwde laag. Deze cyclus gaat laag voor laag door, waarbij het object nauwkeurig van onder naar boven wordt opgebouwd totdat het hele ontwerp compleet is.
7. Afkoelen: Nadat de laatste laag gesmolten is, laat de DMLS machine het gebouwde object langzaam afkoelen in een gecontroleerde atmosfeer. Dit gecontroleerde afkoelingsproces helpt restspanningen en kromtrekken in het onderdeel te minimaliseren, waardoor de maatnauwkeurigheid en structurele integriteit worden gegarandeerd.
8. Steun verwijderen: Net als steigers die in de traditionele bouw worden gebruikt, hebben DMLS-producten vaak ondersteunende structuren nodig om te voorkomen dat kwetsbare onderdelen instorten tijdens het printproces. Deze ondersteunende structuren worden meestal gemaakt van hetzelfde metaalpoeder, maar zijn zo ontworpen dat ze gemakkelijk kunnen worden verwijderd nadat de constructie is voltooid. Technieken zoals machinale bewerking, waterstraalsnijden of mechanische verwijdering kunnen worden gebruikt om deze ondersteunende structuren los te maken, zodat het uiteindelijke metalen object in al zijn glorie zichtbaar wordt.
9. DMLS technologie post-processing: In sommige gevallen kan het nodig zijn om het met DMLS vervaardigde object extra nabewerkingsstappen te laten ondergaan om de gewenste oppervlakteafwerking of mechanische eigenschappen te verkrijgen. Deze stappen kunnen bestaan uit warmtebehandeling voor spanningsontlasting of verbeterde sterkte, zandstralen voor een gladder oppervlak of machinale bewerking voor een hogere maatnauwkeurigheid.
De voordelen en beperkingen van DMLS blootleggen
DMLS-technologie biedt een groot aantal voordelen ten opzichte van traditionele productiemethoden:
- Ontwerpvrijheid: Met DMLS kunnen ongelooflijk complexe geometrieën worden gemaakt, waaronder interne kanalen, roosters en andere ingewikkelde vormen die met traditionele technieken onmogelijk of tegen hoge kosten te maken zouden zijn.
- Snelle prototyping: De mogelijkheid om functionele onderdelen direct vanuit een 3D-model te maken, maakt snelle prototyping mogelijk, waardoor technici ontwerpen snel en efficiënt kunnen herhalen.
- Lichtgewicht: Met DMLS kunnen lichtgewicht structuren met een hoge sterkte-gewichtsverhouding worden gemaakt, waardoor het ideaal is voor toepassingen in de lucht- en ruimtevaart en de auto-industrie.
- Maatwerk: DMLS vergemakkelijkt de productie van op maat gemaakte onderdelen en kleine series, waardoor het perfect is voor gespecialiseerde toepassingen of eenmalige projecten.
DMLS heeft echter ook beperkingen:
- Kosten: DMLS-machines en metaalpoeders kunnen duur zijn, waardoor het proces minder geschikt is voor grote productieseries.
- Beperkingen in bouwgrootte: Het bouwvolume van DMLS-machines is meestal beperkt in vergelijking met traditionele technieken.
- Afwerking oppervlak: Hoewel sommige DMLS-onderdelen een goede oppervlakteafwerking kunnen bereiken, zijn voor andere onderdelen extra nabewerkingen nodig voor een gladder uiterlijk.
- Materiaalbeperkingen: De reeks materialen die beschikbaar zijn voor DMLS evolueert nog steeds, maar breidt zich voortdurend uit.

FAQ
V: Wat is het verschil tussen DMLS en SLS?
A: Zowel DMLS als Selective Laser Sintering (SLS) zijn 3D-printprocessen waarbij een laser wordt gebruikt om laag voor laag objecten te maken. Er is echter een belangrijk verschil in de materialen die ze gebruiken. DMLS werkt met metaalpoeders en smelt deze samen tot een massief object. SLS daarentegen gebruikt meestal kunststof of nylon poeders, waarbij de deeltjes worden gesinterd (versmolten) zonder ze volledig te smelten. Dit verschil resulteert in een aantal belangrijke variaties:
- Materiaaleigenschappen: DMLS-geprinte objecten zijn doorgaans veel sterker en duurzamer dan SLS-onderdelen vanwege de inherente eigenschappen van metaal in vergelijking met kunststof.
- Toepassingen: DMLS is geschikt voor het maken van functionele metalen onderdelen voor de lucht- en ruimtevaart, de auto-industrie en medische toepassingen. SLS blinkt uit in prototyping en het maken van kunststof onderdelen met een goede esthetiek.
- Kosten: DMLS is over het algemeen een duurder proces dan SLS vanwege de hogere kosten van metaalpoeders en de complexere machines.
V: Hoe sterk zijn DMLS-geprinte onderdelen?
A: De sterkte van DMLS-geprinte onderdelen is afhankelijk van het specifieke metaalpoeder en de nabewerkingstechnieken. DMLS-onderdelen kunnen echter ongelooflijk sterk zijn en bereiken vaak mechanische eigenschappen die vergelijkbaar zijn met hun gesmede (traditioneel vervaardigde) tegenhangers. Faktoren zoals warmtebehandeling kunnen de sterkte van het eindproduct verder verbeteren.
V: Wat zijn de opties voor de oppervlakteafwerking van DMLS-onderdelen?
A: DMLS-geprinte onderdelen hebben doorgaans een enigszins ruwe oppervlakteafwerking door de laag voor laag aard van het proces. Er kunnen echter verschillende nabewerkingstechnieken worden gebruikt om een gladdere afwerking te verkrijgen:
- Bewerking: Traditionele bewerkingstechnieken zoals frezen en draaien kunnen worden gebruikt om een gladde en nauwkeurige oppervlakteafwerking te creëren.
- Zandstralen: Deze techniek maakt gebruik van een stroom van schurende deeltjes om het oppervlak van het onderdeel glad te maken.
- Polijsten: Mechanisch of chemisch polijsten kan gebruikt worden om een zeer reflecterende oppervlakteafwerking te verkrijgen.
De keuze van de oppervlakteafwerking hangt af van de gewenste esthetiek en functionele eisen van het uiteindelijke onderdeel.
V: Wat zijn de milieuoverwegingen van DMLS?
A: DMLS heeft, net als elk productieproces, gevolgen voor het milieu. Hier zijn enkele belangrijke factoren om rekening mee te houden:
- Energieverbruik: DMLS-machines hebben een aanzienlijke hoeveelheid energie nodig om de krachtige laser te laten werken en een gecontroleerde atmosfeer te handhaven.
- Materiaalafval: Afhankelijk van de geometrie van het onderdeel en het ontwerp van de ondersteuningsstructuur, kan er wat metaalpoeder verloren gaan tijdens het DMLS-proces. Sommige machines bieden echter mogelijkheden voor poederrecycling om verspilling tot een minimum te beperken.
- Uitstoot: Bij het DMLS-proces kunnen kleine hoeveelheden stof en rook vrijkomen, afhankelijk van het materiaal dat wordt geprint. Een goed ventilatiesysteem is cruciaal om deze uitstoot te beperken.
Fabrikanten streven er voortdurend naar om de efficiëntie en duurzaamheid van DMLS-technologie te verbeteren. Er wordt voortdurend onderzoek gedaan om energiezuinigere machines te ontwikkelen en de afvalproductie te minimaliseren.
De toekomst van DMLS: Een blik op de innovaties van morgen
DMLS-technologie ontwikkelt zich snel en verlegt voortdurend de grenzen van wat mogelijk is. Hier zijn enkele opwindende trends die de toekomst van DMLS vormgeven:
- DMLS voor meerdere materialen: De mogelijkheid om objecten te printen met meerdere metaalpoeders binnen dezelfde build opent deuren voor het maken van onderdelen met unieke combinaties van eigenschappen.
- Grotere bouwvolumes: DMLS-machines met een groter bouwbereik zijn in ontwikkeling, waardoor nog grotere en complexere metalen voorwerpen gemaakt kunnen worden.
- Snellere printsnelheden: Vooruitgang in lasertechnologie en poederbehandelingsmechanismen leidt tot snellere printtijden, waardoor DMLS efficiënter wordt voor productietoepassingen.
- Nieuwe materialen: De reeks materialen die compatibel zijn met DMLS breidt zich voortdurend uit, inclusief nieuwe legeringen en zelfs exotische materialen zoals titanium aluminide (TiAl).
De DMLS technologie blijft zich ontwikkelen en heeft het potentieel om een revolutie teweeg te brengen in verschillende industrieën, van de lucht- en ruimtevaart en de auto-industrie tot de medische sector en daarbuiten. Met de mogelijkheid om complexe, functionele en lichtgewicht metalen onderdelen te maken, is DMLS klaar om een belangrijke rol te spelen in het vormgeven van de toekomst van de productie.